Our commitment to dyeing
What is "Edo Komon®" dyeing?
"Breathtakingly beautiful" traditional crafts
Komon refers to kimonos dyed with intricate or small patterns.
Among them, "Edo Komon®" uses intricate and detailed "Ise Katagami" that is carved by skilled artisans in the Ise region using their techniques, and highly skilled artisans who are certified as traditional craftsmen in Tokyo use a dye-resistant paste and a spatula-dyeing technique called kata-uri.
The exquisite Edo Komon®, which is the culmination of the finest techniques, is said to be breathtakingly beautiful, and the techniques and sensibilities cultivated over a long tradition are still being passed down by talented successors.
Contemporary Master Craftsman, Yellow Ribbon Medal
"Edo Komon®" Dyeing
The special features of the "Daimatsu Dyeing Factory"
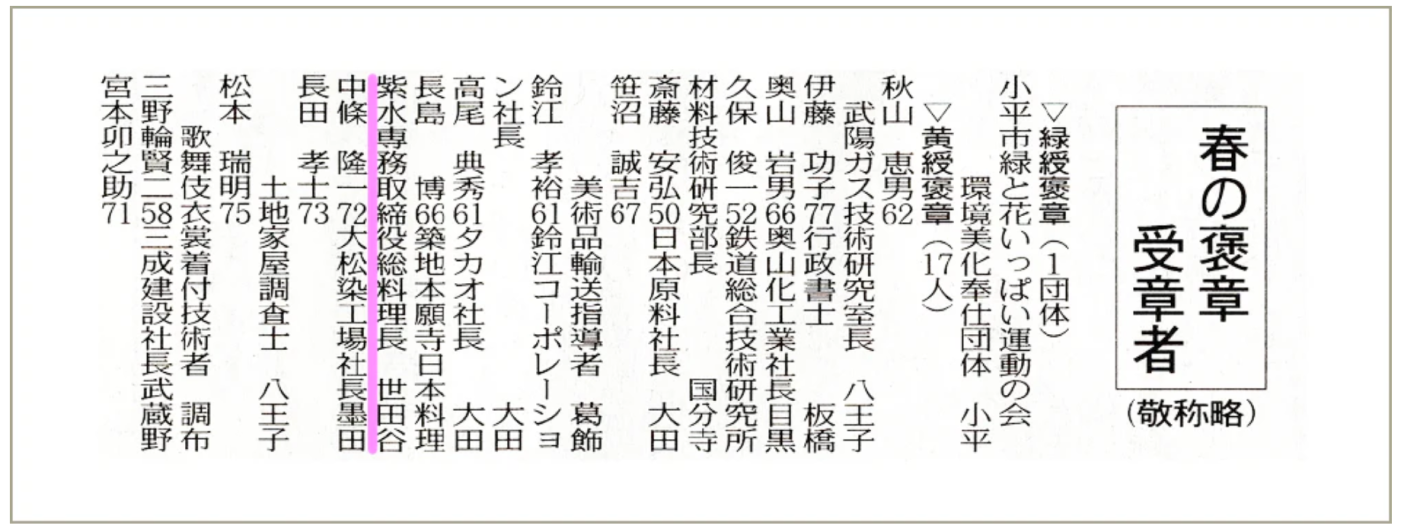
What is the special "Edo Komon®"?
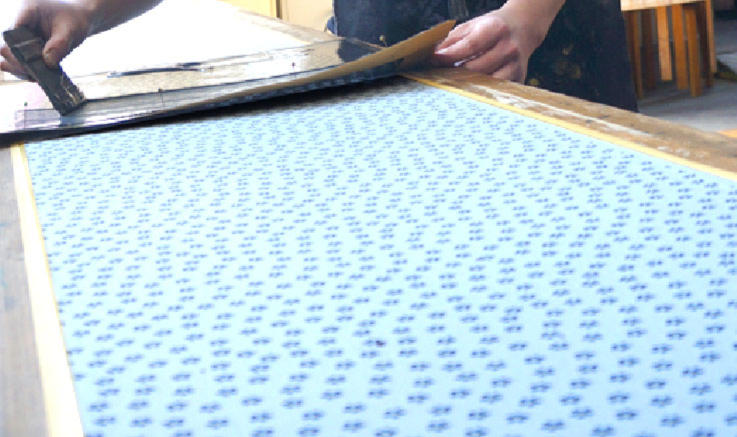
Received the Yellow Ribbon Medal
K-iwami bags are dyed by Ryuichi Nakajo, a traditional craftsman at the Daimatsu Dyeing Factory in Sumida Ward, Tokyo, who has been awarded the Yellow Ribbon Medal.
Most of the dyers who dye "Edo Komon®" have the skills to dye silk, but do not have the techniques to dye other materials.
Daimatsu Dyeing Factory has the techniques to dye not only kimonos, but also other materials using the "Edo Komon®" dyeing technique.
This is the elegant and beautiful "Edo Komon®" dyeing technique that is "particular" and can only be found here.
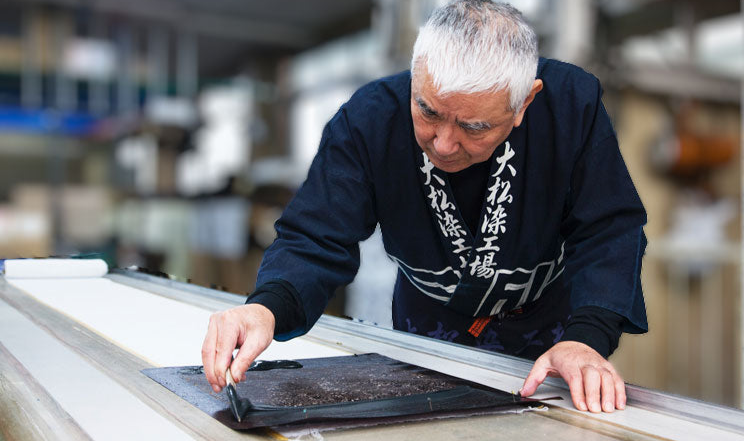
Traditional craftsman "Ryuichi Nakajo"
It may be a new era, but I want people to wear kimonos, a traditional Japanese culture.
Nakajo also wants many people to learn the advanced traditional Japanese techniques of hand-dyeing and pass them on to future generations.
To that end, I have been studying dyes since I was young, hoping to develop new products using this technology and have them used in modern life, spreading the word about the greatness of "Edo Komon®" dyeing.
By using "Edo Komon®" to produce products other than kimonos, we hope to pass on the traditional culture of the Japanese people to future generations.
The origins of "Edo Komon®"

It all started in the Muromachi period
It was first used in the Muromachi period on the leather parts of armor and for family crests, and it is believed that it was not until the late Muromachi period that it began to be used on everyday clothing worn by armored personnel carriers.
At the beginning of the Edo period, it was started to dye the formal attire of samurai, the kamishimo, and the technique developed and spread widely. In the mid-Edo period, with the development of townspeople's culture, komon became beloved by ordinary people, regardless of social status or time, and has remained so to this day.
In 1955, to distinguish it from Kyo Komon and Kaga Komon, the word Edo was added and "Edo Komon®" became the official name for Tokyo dyed fabric.
We hope that the sensibility and techniques cultivated over a long tradition will be passed down by talented successors, and that this will continue to be passed down as a traditional craft that Japan can be proud of.
How "Edo Komon®" is made
-
1. Carving stencils
Button LabelTwo or three sheets of high-quality handmade washi paper are glued together with persimmon tannins to form the "base paper," and patterns are carved into the paper using an awl (tsuribori), a small knife (tsukibori/hikibori), tools (dogubori), etc. This stencil is itself a work of art.
-
2. Adjusting the color paste
Button LabelColor paste is important as it determines the quality of the dyed fabric. There are two colors: base color and eye color. First, glutinous glutinous rice flour and rice bran are mixed and steamed, and the dye is added to the well-kneaded base paste, which is then carefully dyed with a test dye.
-
3. Shaping and drying on a board
Button LabelWhite fabric is stretched over a long board, a stencil is placed on top of it, and glue is applied with a spatula. The pattern is imprinted on the fabric only in the areas carved out by the stencil, and this is the most important part of the dyeing process. After the imprinting is complete, the glue is left to dry on the board.
Multi-Column
-
4. Ground color dyeing (shigoki)
Button LabelOnce the paste has dried, the fabric is removed from the board and the dye-containing paste is applied evenly over the entire surface with a spatula to dye it in the base color. This is called "shigoki". After that, sawdust powder is sprinkled on top of the base dye (shigoki) to prevent the paste from sticking to the other parts.
-
5. Steaming
Button LabelBefore the base color dries, the fabric is placed in a steamer and steamed at 90-100 degrees for 15-30 minutes. This is to fix the dye in the starch to the fabric, and the degree of steaming requires skill.
-
6. Wash and dry
Button LabelThe steamed fabric is thoroughly washed in water to remove starch and excess dye. The washed fabric is then dried, boiled in water to adjust the width, and carefully inspected and finished before being dyed.
Sumida Brand Certification
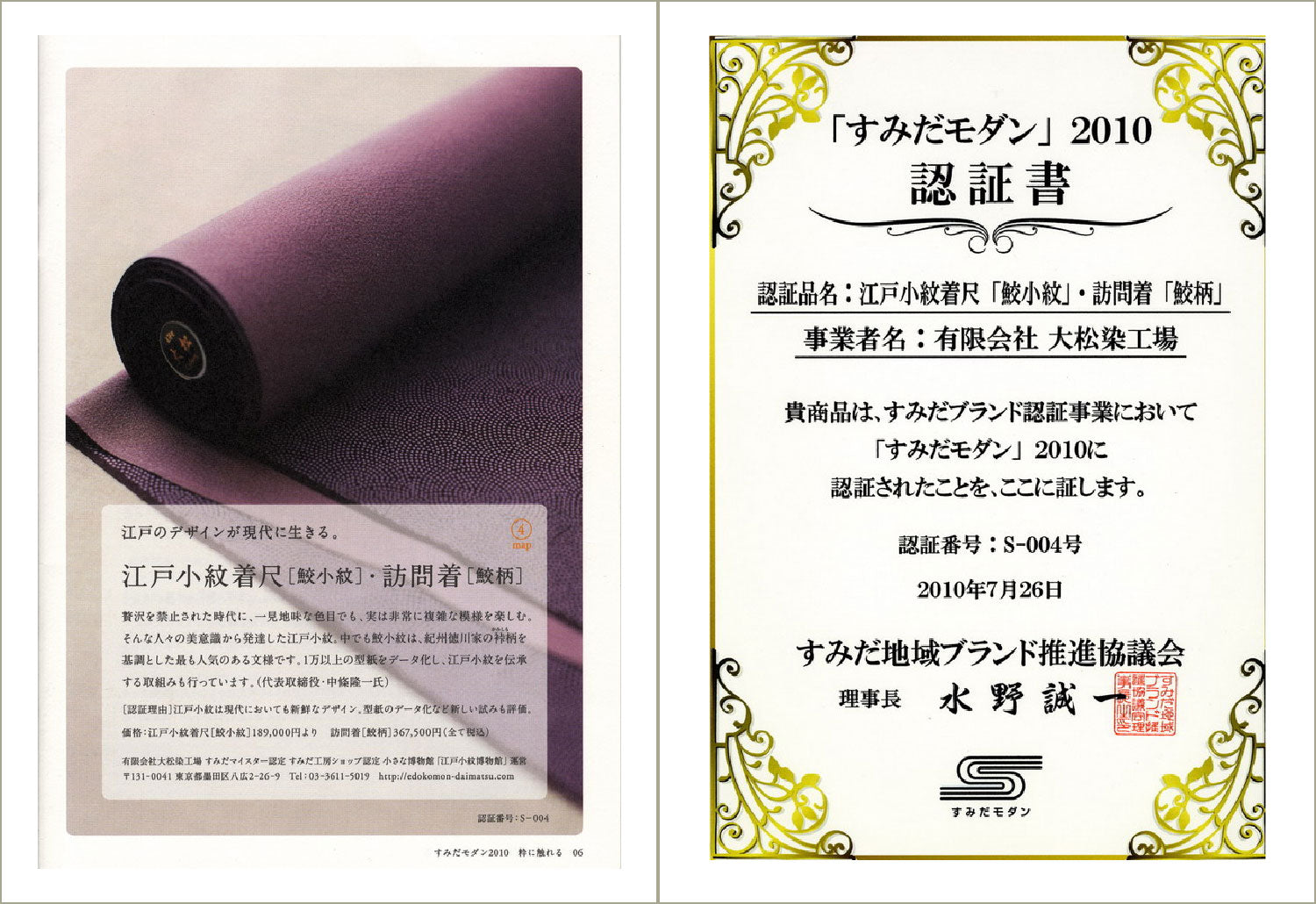
For those who want to see more
-
Ultra-lightweight fiber "Kaminoito®"
What is "Kaminoito®"?At the time of development, the fabric was woven with Kaminoito®, an ultra-lightweight fiber produced by a spinning company in Izumo. The material is highly breathable, absorbent, quick-drying, and durable, and has deodorizing, antibacterial, and cooling properties, making it a material that can be used for a long time.
-
Dyeing technique "Edo Komon®"
What is "Edo Komon®"?Fabric woven with "Kaminoito®" has been designated by the Minister of Economy, Trade and Industry and dyed using the traditional dyeing technique "Edo Komon®" to create beautiful patterns, which have also been adopted as the emblem mark for the Tokyo 2020 Olympics.
-
Sewing master "Hajimezawa"
What is the "Hajimezawa Bag"?The skilled bag craftsmen at Hajimezawa Bags, led by representative Hajimezawa Kenji, and employees with expert techniques and sewing sense, carefully and precisely sew each bag with care and attention to detail.